ππ§ππ£π§πππ¨ | πππ‘π π£π₯ππππ π π πππ
Inline Inspection (ILI) is a crucial technique used in the maintenance and assessment of pipelines. It involves the use of tools known as smart pigs that travel through the pipeline to collect data on its condition. This technology helps in identifying defects, corrosion, and other anomalies that could potentially lead to pipeline failures.
Pipelines are vital for transporting oil, gas, and other materials over long distances. Ensuring their structural integrity is paramount to prevent leaks, spills, and catastrophic failures.
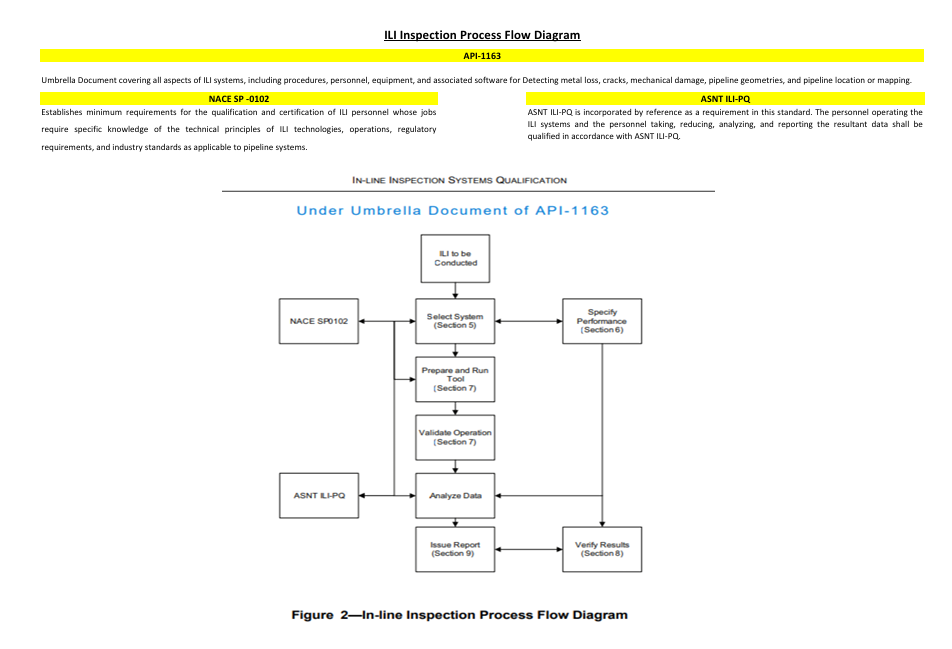
βπππππππ ππ πππ βπ£π ππππ₯
β
Β Pre-Inspection Preparation
Pipeline Data Collection: Gather detailed information about the pipeline, including its age, material, diameter, length, operating pressure, and previous inspection or maintenance records.
Tool Selection: Choose the appropriate ILI tool based on the type of pipeline and the specific defects to be detected. Common ILI tools include magnetic flux leakage (MFL), ultrasonic testing (UT), and electromagnetic acoustic transducers (EMAT).
β
Β Inspection Execution
Cleaning the Pipeline: Clean the pipeline to remove any debris that could interfere with the ILI tool’s operation.
Running the ILI Tool: Deploy the ILI tool into the pipeline. The tool is propelled by the flow of the product (oil, gas, etc.) and collects data as it travels through the pipeline.
β
Β Data Analysis and Reporting
Data Retrieval: Retrieve the ILI tool and download the collected data for analysis.
Data Analysis: Analyze the data to identify any defects, corrosion, or anomalies. Advanced software and algorithms are often used to interpret the data accurately.
Reporting: Generate a detailed report outlining the findings, including the location, size, and severity of any detected defects.

βπ π€π₯ πππ€π‘πππ₯ππ π πΈππ₯ππ§ππ₯πππ€
β
Β Assessment and Prioritization
Defect Assessment: Assess the severity of the detected defects and prioritize them based on the potential risk they pose to the pipeline’s integrity.
Repair Plan: Develop a repair plan to address the critical defects. This plan should include the methods, materials, and timeline for repairs.
β
Β Maintenance and Monitoring
Scheduled Maintenance: Schedule regular maintenance activities based on the findings of the ILI report.
Continuous Monitoring: Implement continuous monitoring systems to track the condition of the pipeline and detect any new defects early.
β
Β Documentation and Review
Documentation: Document all inspection, repair, and maintenance activities comprehensively.
βπ ππππ¦π€ππ π
The insights gained from ILI help in making informed decisions about pipeline maintenance, ensuring long-term operational efficiency and safety.