Introduction
Sleeve welding is a widely used method for reinforcing and repairing pipelines, ensuring their integrity and longevity. Compliance with ASME PCC-2 (Repair of Pressure Equipment and Piping) is crucial to achieving safe and effective repairs. This article explores sleeve welding as per ASME PCC-2, its benefits, welding procedures, and best practices to ensure pipeline reliability.
What is Sleeve Welding?
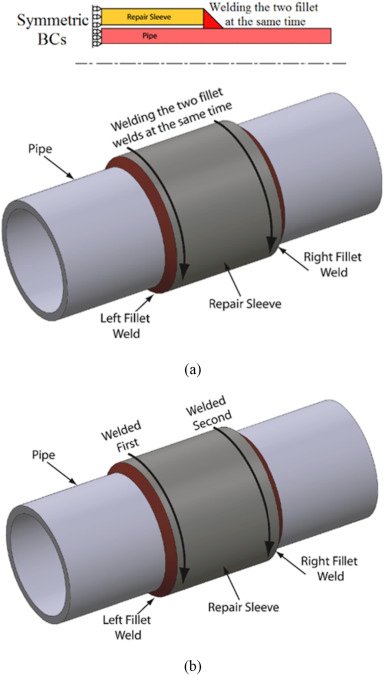
Sleeve welding is a repair technique where a steel sleeve is installed over a damaged pipeline section to restore its strength. The sleeves can be either full-encirclement or partial-encirclement, depending on the defect severity and repair requirements. This method is commonly used to repair corrosion defects, cracks, and mechanical damages without shutting down the pipeline.
ASME PCC-2 Compliance in Sleeve Welding
The ASME PCC-2 standard provides guidelines for designing, fabricating, and installing welded sleeves. Compliance with this standard ensures that repairs meet industry best practices, safety regulations, and structural integrity requirements.
Key ASME PCC-2 Requirements for Sleeve Welding
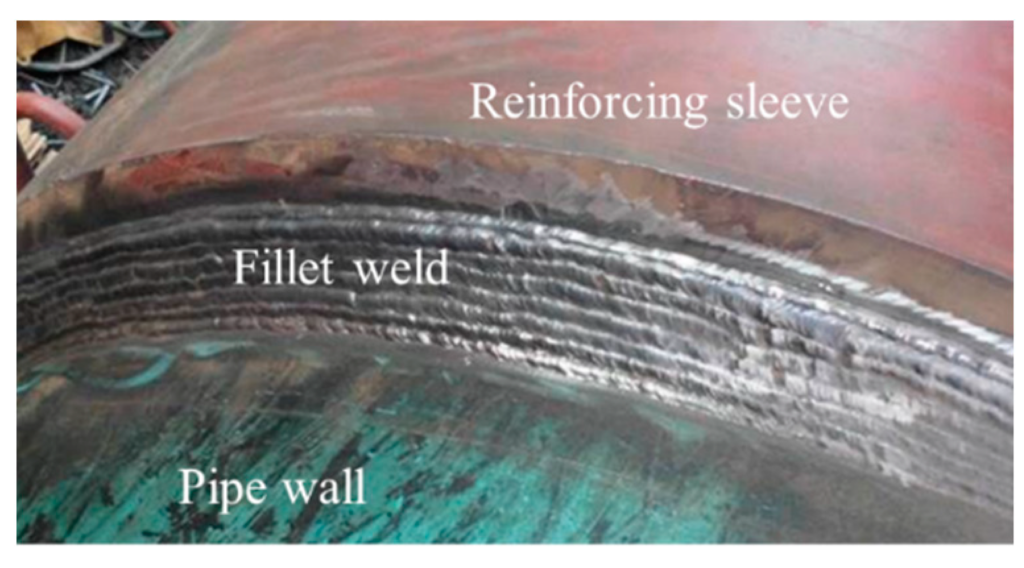
Material Selection:
Sleeves should be made of materials compatible with the pipeline (e.g., API 5L, ASTM A106, or ASTM A516 Grade 70).
The welding electrode or filler material should match or exceed the mechanical properties of the pipe material.
Welding Procedure Qualification:
Welding procedures must be qualified as per ASME Section IX.
Pre-weld and post-weld inspections are necessary to ensure quality and compliance.
Weld Design & Joint Preparation:
Sleeves should be beveled to allow for strong weld penetration.
The fillet welds should be sized appropriately to withstand operational stresses.
NDT & Inspection Requirements:
Non-Destructive Testing (NDT) techniques like ultrasonic testing (UT), radiographic testing (RT), and magnetic particle testing (MT) should be used to verify weld quality.
Visual inspections should confirm full weld fusion and absence of defects.
Stress Relief and Coating Protection:
If required, post-weld heat treatment (PWHT) should be performed to relieve residual stresses.
The welded sleeve must be coated to prevent corrosion and ensure long-term durability.
Step-by-Step Sleeve Welding Procedure
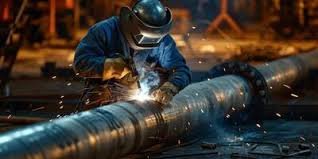
Pipeline Preparation:
Clean the defective area to remove contaminants, rust, and coatings.
Conduct thickness measurement to assess pipeline integrity.
Sleeve Fabrication & Installation:
Cut and prepare the sleeve to the required size.
Position the sleeve over the pipeline defect and secure it using clamps.
Welding Execution:
Perform root pass welding and fill passes using an approved welding technique (e.g., SMAW, GTAW, or GMAW).
Ensure controlled inter-pass temperatures to prevent cracking.
Post-Weld Inspection & Testing:
Conduct NDT methods to check weld integrity.
Perform hydrostatic testing if required by project specifications.
Final Coating & Restoration:
Apply corrosion-resistant coatings such as epoxy or polyurethane-based coatings.
Restore the pipeline to full operational service after clearance.
Advantages of ASME PCC-2 Compliant Sleeve Welding
Minimizes Downtime: Repairs can often be performed without pipeline shutdown.
Cost-Effective: Avoids expensive pipeline replacements.
Enhanced Structural Integrity: Strengthens weak sections and prevents failures.
Regulatory Compliance: Meets industry safety and reliability standards.
Extended Pipeline Life: Provides long-term reinforcement against corrosion and defects.
Conclusion
ASME PCC-2 compliance in sleeve welding ensures a high-quality, safe, and durable pipeline repair process. By following material selection, welding procedure qualification, NDT inspection, and coating protection guidelines, operators can maintain pipeline integrity effectively. Implementing ASME PCC-2 best practices not only ensures regulatory compliance but also enhances pipeline longevity and operational safety.
For more insights into pipeline repair methods and compliance standards, stay tuned to our blog or reach out for expert guidance on ASME PCC-2 welding solutions.